The world is changing rapidly due to an electric vehicle (EV) revolution that is currently underway. This is no longer an urban phenomenon or something that was long considered a pet project of developed nations. Various sectors such as; (i) Electronics and internet, (ii) logistics and transportation, (iii) agriculture and medicine, (iv) energy and infrastructure, and (v) defence and aerospace, have all been forced to innovate and adapt to this changing world order. Standalone electric platforms are currently being envisioned and built for applications ranging from urban land/sea/air mobility, defence, personal automotive, mass transit and all the way to unmanned aerial vehicles for rural crop -health maintenance and monitoring, -security and -damage mitigation. At the core of this revolution, lies the technology that catalyzed all of this – the electrochemical rechargeable battery. Through several decades of systematic R&D involving a global network of scientists and entrepreneurs, this technology has come a long way, yet not far enough. Batteries have become so intertwined with our way-of-life, so much so that they have transitioned from being a technology driver to the driver of any nation’s strategic interest and positioning in the times ahead.
Globally, various battery systems are currently explored in the R&D space which includes lithium-ion, sodium-ion, alkali-metal, multivalent-ion, alkali-sulfur, alkali-air, all solid-state and flow cells. Despite the numerous options, lithium-ion batteries (LIB) owing to their versatility in choice of chemistries, ease of manufacturing and reliable performance metrics, have seen the broadest commercial deployment. The dream of a sustainable future with wide implementation of renewable technologies in sync with associated energy storage powered by LIB looks enticing, but, unfortunately this is extremely challenging to achieve. This is because, modern LIBs contain a lot of elements such as Lithium, Cobalt and Nickel that can be considered critical in terms of their supply chain and ease of cost-effective availability.
For years, one of the overarching goals of R&D in batteries has been reducing the cost of cells to facilitate wider commercial adoption. As a consequence, battery manufacturing is heavily reliant on the principle of economy of scale – where, the more batteries produced, the more profit made. Thus, the quest globally has been the setting up of Giga Factories which can cater to the to a rapidly growing need. The most conservative projections estimate over 150 million electric vehicles on road by 2030 across the world and this requires an enormous amount of batteries and hence establishing more giga factories are often the way to go. In terms of types of batteries (LIBs) that can be manufactured, the options are straightforward at present. Presently, around 40% of the cost of modern LIBs go towards cathodes and thus, we can broadly classify the type of LIB based on the cathode material employed. Battery types categorized based on cathodes employed, that hold the vast majority of global market share include; (i) Lithium Iron Phosphate (LFP) class, (ii) Lithium Nickel Cobalt Manganese Oxide (NMC/NCM) class, (iii) Lithium Cobalt Oxide (LCO) class. LFP based batteries have excellent safety and cost advantages however, when compared to the NMC and LCO types, they lack energy density which is the metric that governs how far an electric vehicle can go before needing to stop for a recharge. LCO types offer higher energy densities and were the cathode of choice for some of the earliest commercially available batteries, however their cost and power densities have made them less attractive as years go by. NMC types are versatile cathodes which offer a whole gamut of compositions (LiNixMnyCozO2, where x+y+z=1) that can be customized based on the type of end-use application in addition to their higher energy densities. Keeping differences between these cathode classes aside, all these chemistries contain materials that are considered critical due to their global demand, availability and supply chain constraints (Lithium in LFP; Lithium and Cobalt in LCO; and Lithium, Cobalt and Nickel in NMC). Among these critical elements, the state of Cobalt is most concerning from a battery manufacturing perspective. If one was to rank the order of criticality in battery raw materials, the most critical would be Cobalt followed by Nickel and then Lithium. Known global cobalt reserves currently total at approximately 8 million metric tonnes. If no new sources of cobalt are discovered, then considering the pace at which EV projections are proposed, we would run out of usable cobalt for battery industry by 2050.
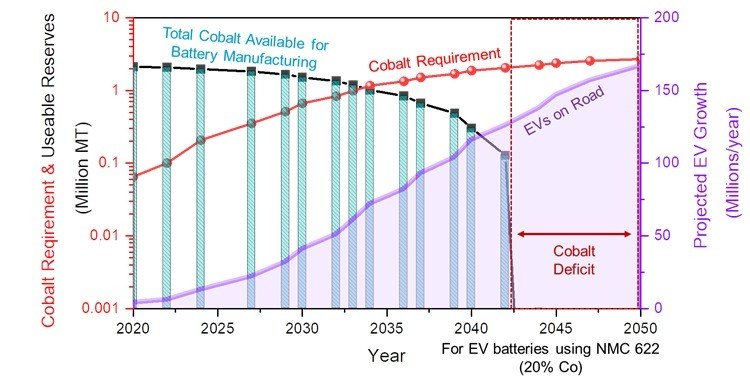
Fig. 1: Data from BatPAC Model highlighting the depletion of global cobalt reserves
Additionally, cobalt prices have been constantly fluctuating in the past decade with prices nearly tripling in recent years which is unsustainable for battery manufacturing companies where profitability depends on economy of scale.
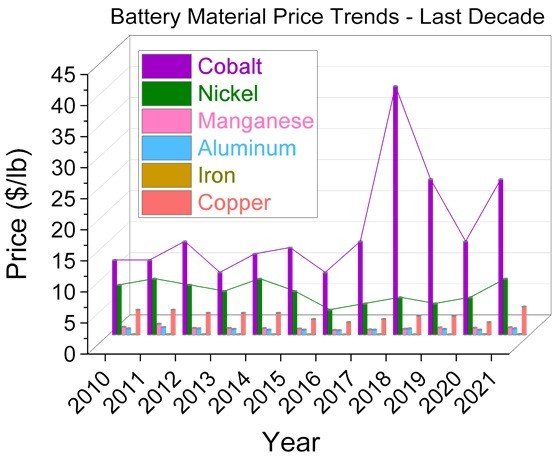
Fig. 2: Price trends for materials used in battery manufacturing from 2010 to 2021
Thus, it should be noted that installation of battery manufacturing infrastructures without adequately securing long-term raw material supply chains for critical elements making up the composition of the cathodes would not lead to the long envisioned sustainable future. Moreover, strategies to mitigate impact of price fluctuations and supply chain constraints, such as recycling existing LIBs in an efficient and sustainable manner should be prioritized in addition to the quest for new critical material free battery chemistries.
For an emerging economy like India, currently most of our battery cell and material requirements are met through significant imports from countries like China. With the nation’s quest for realizing a sustainable future, through its target of achieving net zero by 2070, the onus would be on quickly developing and deploying sustainable technologies such as EV platforms powered by locally manufactured batteries. Thus, home-grown battery materials (cathode and anode) with less critical materials employed, coupled with effective recycling of existing batteries would be the ideal approach. In this regard, there has been consistent efforts towards setting up giga factories in the country for catering to the battery requirement via local manufacturing. However, there is a strong need for setting up cathode/anode material production plants and developing local expertise that can feed these upcoming battery manufacturing giga factories with both good quality material in addition to reliable and talented workforce. There is also a need to develop accompanying R&D infrastructures and programs that are focussed on facilitating a seamless transition of newly developed battery materials and prototype devices from lab scale to pilot scale and beyond.
Our goal should be to develop new cathode/anode chemistries that employ less or sometimes none of the critical elements and to assemble next-generation batteries that demonstrate good performance metrics. They should be viable for commercial transition without requiring a complete overhaul of existing and upcoming giga-scale battery manufacturing factories.
References:
[1] Muralidharan, N., Self, E. C., Dixit, M., Du, Z., Essehli, R., Amin, R., … & Belharouak, I. (2022). Next‐Generation Cobalt‐Free Cathodes–A Prospective Solution to the Battery Industry’s Cobalt Problem. Advanced Energy Materials, 12(9), 2103050.
[2] Muralidharan, N., Self, E. C., Nanda, J., & Belharouak, I. (2022). Next‐generation cobalt‐free cathodes–a prospective solution to the battery industry’s cobalt problem. Transition Metal Oxides for Electrochemical Energy Storage, 33-53.
Author – Nitin Muralidharan, PhD, Assistant Professor, Chemical Engineering, Indian Institute of Technology – Madras